5 Safety Strategies to Scale Down Your Workers’ Comp Spending
March 1st, 2023 | 6 min. read
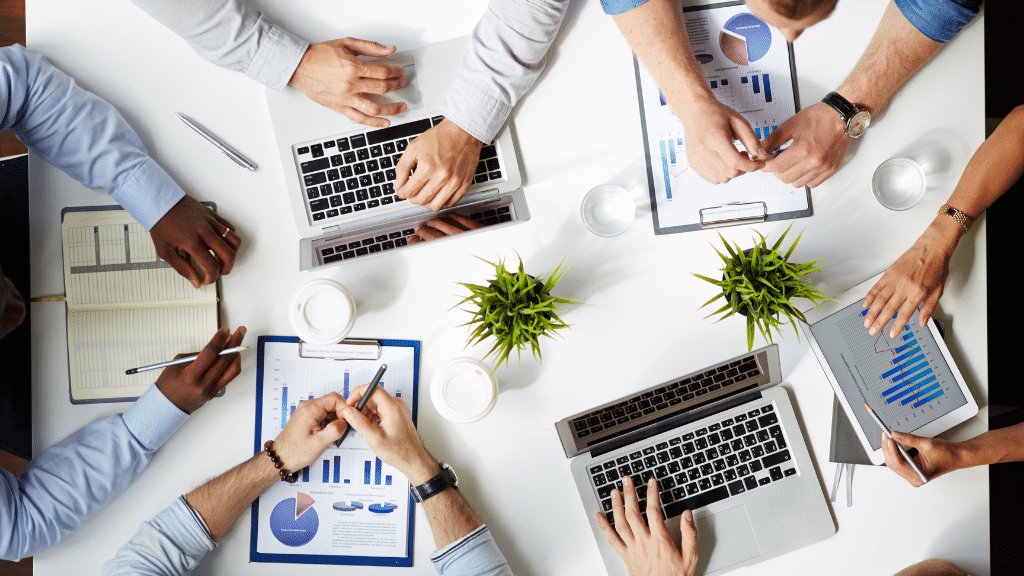
We’ve all heard the phrase, “a penny saved is a penny earned.”
Because earning is the underlying goal of operating a business, it is important for you to identify areas where you can actively save your pennies.
But with employer expenses ranging from labor to benefits and social security to taxes, isolating these profitable areas can be challenging.
Cutting your labor cost will slash employee salaries – You can’t do that. Downsizing your benefits program will diminish your ability to recruit and retain a capable workforce – You can’t do that. Need we even talk about evading taxes – You certainly can’t do that.
So, then, what CAN you do to save money while also positively impacting your business operations?
Reduce your workers’ comp coverage cost by developing and implementing better safety protocols.
It’s safe to say that, here at Combined, our commercial insurance experts understand the correlation between sound safety standards and reduced workers’ comp costs. Having helped many employers minimize their workers’ comp expenses, we are committed to teaching you how you can too.
In this article, we will discuss how focused safety measures can help you curb your workers’ comp costs. By reading it, you will learn 5 steps you can take to scale up the success of your workplace safety policies while scaling down your workers’ comp coverage spending.
A common misconception – Avoiding accidents is the key to reducing workers’ comp costs
It seems logical enough. Because the amount and severity of insurance claims affect the price of your workers’ comp premium, avoiding accidents should equate with cheaper coverage.
But is just avoiding the occurrence of accidents enough to prevent them from happening?
Think of it like this:
A neighborhood has a busy 4-way intersection with no stoplights or signs – and, it is universally understood, that everyone passing through wants to avoid a collision.
What will happen?
Without traffic being directed, it is just a matter of time before the intersection looks like an amusement park bumper car attraction.
Workplace accidents work the same way. You can do your best to avoid them, but without an effective system to prevent them, it’s just a matter of time before they happen.
And as they happen, the price of your workers’ comp premium rises.
The key to reducing workers’ comp costs is establishing and implementing solid safety standards
Back to our unregulated 4-way intersection:
The easiest way to prevent accidents from happening is to install a signal. With intersection traffic guided by changing colored lights, accidents will be few and far between.
Again, workplace accidents work the same way. By establishing a standard for workplace safety and implementing a system to regulate it, you’ll experience fewer on-the-job incidents. This is the workplace equivalent of installing a stoplight.
And fewer work-related accidents means fewer dollars spent on workers’ comp insurance.
5 steps to scale up workplace safety and scale down workers’ comp spending
So, how do you establish a standard for workplace safety and implement a regulatory system for it?
These 5 steps will guide you toward achieving just that.
1. Put an Occupational Safety and Health Administration (OSHA) compliant safety program in place – and make it a priority
As part of the United States Department of Labor, OSHA outlines and enforces workplace safety standards. By federal law, OSHA requires employers to provide employees with a safe work environment. This is defined as a “workplace free from known health and safety hazards.”
The standards to provide and maintain a safe work environment vary by industry and job description, so staying up-to-date with industry-specific safety criteria is essential.
But, one OSHA standard that is constant across all industries, is developing a written safety program and communicating it with all employees.
In order to be effective and OSHA-compliant, this safety program should:
- Detail your company’s safety policies and procedures including how to identify, control, and prevent workplace hazards as well as define an appropriate emergency response
- Express your company’s position on the importance of safety
- Assert your company’s expectations for adherence to safety protocol
By fully developing, communicating, and prioritizing a sound safety program, your workforce will be informed of your safety policies and procedures, and these safety policies and procedures will be more readily followed.
2. Promote company-wide participation – because everyone plays a part in safety
Now that you’ve developed and implemented a sound safety program, you want to make sure that your entire workforce – from CEO to unpaid intern – abides by it.
Where “a chain is only as strong as its weakest link,” your safety program is only effective if its policies become company-wide practices.
Here are a few ways to make sure that your written policies turn into consistent practices:
- Emphasize education in safety protocol for managers and supervisors:
If your leaders exemplify the pillars of your safety program, so too will the rest of your current workforce.
- Incentivize adherence to safety policies and procedures:
Nothing is better encouragement to follow rules than being rewarded for it. Positively reinforcing adherence to safety policies will create good safety practices and solidify them as long-term habits.- Incorporate safety training into your onboarding process:
The best place to start is at the beginning. By incorporating safety training into the early stages of employment, you make sure that safety policies and procedures are a priority for your new employees from the get-go.
The best place to start is at the beginning. By incorporating safety training into the early stages of employment, you make sure that safety policies and procedures are a priority for your new employees from the get-go.
3. Report all accidents and injuries – then identify the causes behind problems
The occurrence of accidents and injuries is unfortunate, but the data they lend you is not. Should any incidents occur, no matter the severity, make sure that they are reported.
Your accident reports tell you what happened. But they also allow you to investigate and identify why it happened.
And, once you know the why behind past accidents, you can place a focused preventative effort on those exact areas. In a way, your accident reports allow you to zone in on problem areas and work toward solutions.
Reporting all work-related accidents, especially small ones, is stigmatized – because a larger number of claims corresponds to a higher workers’ comp insurance premium, many employers shy away from this practice. In doing so, they condemn the same accidents to be repeated.
However, if you use these reports to find the root causes of regularly occurring accidents and fix them, you avoid the same accidents from continually happening again and again.
You should report all incidents and near-misses and then use them as progressive tools for safety training.
According to OSHA, “addressing underlying or root causes is necessary to truly understand why an incident occurred, to develop truly effective corrective actions, and to minimize or eliminate serious consequences from similar future incidents.”
In a perfect world, you’d isolate all problem areas and adopt effective solutions to them, and accident occurrence would be no more.
While I cannot guarantee this result, with agreement from the United States Department of Labor, I can say that reporting and investigating accidents that occur in the workplace is crucial to preventing them from happening in the future.
And, because fewer claims, mean a lower workers’ comp insurance premium, this tried-and-true method can reduce your workers’ comp spending in the long run.
4. Perform a regular claims review – and use it to improve your safety program
Following a claims review, you have invaluable insight into the cost of your workers’ comp premium.
Because claims affect the cost of your premium, reviewing this cost and contributing claims allows you to isolate areas where you can improve your safety program.
With this in mind, a claims review allows you to correct inadequate safety policy and procedure, minimize claims, and reduce the cost of your coverage premium in the future.
5. Repeat these steps regularly – and produce a sound safety culture
Once you’ve established and implemented a workplace safety standard, you just have to continue to build upon this foundation.
If you do this, you will cultivate a company-wide culture rooted in sound safety practices.
How do you do this?
By treating these steps like an ongoing improvement cycle – routinely repeating and applying them to your workplace safety protocol.
Following a claims review, take what you’ve learned and apply it by:
- Updating your OSHA-compliant safety program
- Promoting company-wide participation in your updated safety program
- Reporting and identifying the causes of all accidents that occur under your updated safety program
- Learning how you can improve upon your updated safety program from a claims review
- Taking what you’ve learned from every claims review to repeat these steps
And, with a company-wide safety culture, workplace safety has nowhere to go but up and your workers’ comp cost has nowhere to go but down.
Take the next steps toward safety standards that will reduce your workers’ comp spending
If you are here, the tug-of-war between reducing business costs and maintaining optimal operations is a never-ending conflict.
You want to do both – but the two just don’t seem to go hand-in-hand.
By reading this article, you learned that attention to workplace safety can not only improve on-the-job operations but also reduce the cost of workers’ comp coverage.
Here at Combined, our commercial insurance experts have helped countless employers understand how the cost of workers’ comp insurance and better workplace safety protocol do work together. We want to help you use a sound safety strategy to save on your workers’ comp spending.
![]()
|
Schedule an appointment with a team member to learn how to turn safety into savings. |
![]() |
If you are not yet ready to speak with a team member, you may find these resources helpful: |
This article is not intended to be exhaustive nor should any discussion or opinions be construed as legal advice. Readers should contact legal counsel for legal advice.